Obsessed with quality – the details
Many people ridicule us Germans for being so meticulous and detail-oriented – millions of practitioners love us for it!
We live and breathe quality. In everything that we do: every product we make. Every lens we polish. Every screw we tighten. Every optic fiber we bundle. Quality is always at the forefront of our minds, every single day.
The durability of our instruments is legendary. Every single instrument is the result of decades of product development, continuous improvements, production and a 100 % quality control in our own facilities. We thoroughly ensure that our high expectations of quality are maintained.
That way we also ensure that our claim for our high-end products – that they allow for “the most accurate diagnosis, as early as possible” – is also met.
No more, no less.
Think global. Produce local.
All HEINE instruments – otoscopes, laryngoscopes, loupes, lights, ophthalmoscopes, dermatoscopes, sphygmomanometers and more – are fully manufactured in Germany, on our premises in Gilching, south of Munich. And we will continue with our local manufacturing efforts in future too.
Just over 90% of vendor parts come from Germany. Indeed, 45% come from Bavaria and southern Germany. We even develop and manufacture the control electronics for our lithium-ion batteries and LEDHQ ourselves on site.
This has the additional welcome benefit that we save ourselves transport costs and cut back on the amount of harmful emissions released into the environment.
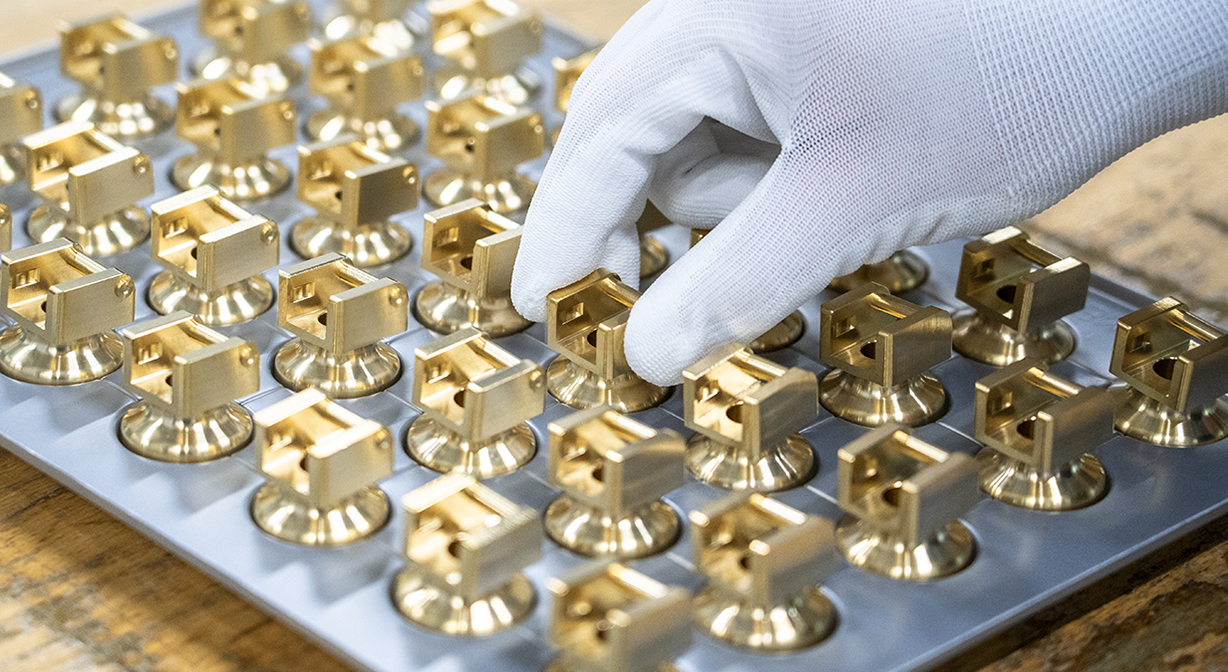
Vertical integration
We prefer to rely on ourselves.
One of the most important cornerstones of our corporate philosophy is our high level of vertical integration. From the idea to the finished product, all relevant work steps are performed in-house, i.e. directly on HEINE’s premises.
For example, all products are developed and perfected in our own Research and Development Department.
Then, in our Tool and Mould Construction Department, we design and manufacture injection moulds, as well as the tools required for the manufacturing process.
In Plastics Production, we produce housing parts and the tips for our otoscopes and, in our in-house electroplating plant, we coat and refine a multitude of metallic components.
The next step is Optics Production.
When it comes to quality, we really do split hairs.
Our lenses, for example, are manufactured in our very own Optics Production Department that combines German craftsmanship with state-of-the-art CNC-controlled machines.
Many of the lenses are manufactured with an accuracy of +/- 0.0001 mm, which is 20 times less than the diameter of a human hair.
Incidentally, in the Optics Department alone, more than 26,000 lenses, mirrors and other optical components are manufactured every month. So our name – HEINE Optotechnik – is no coincidence.
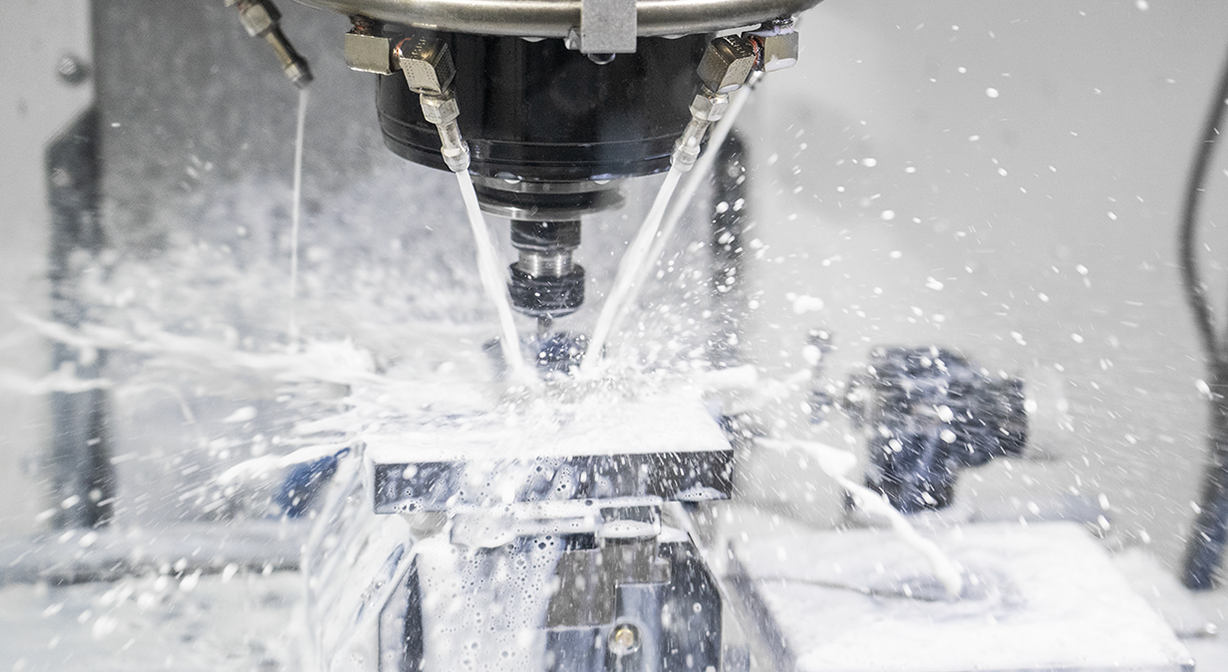
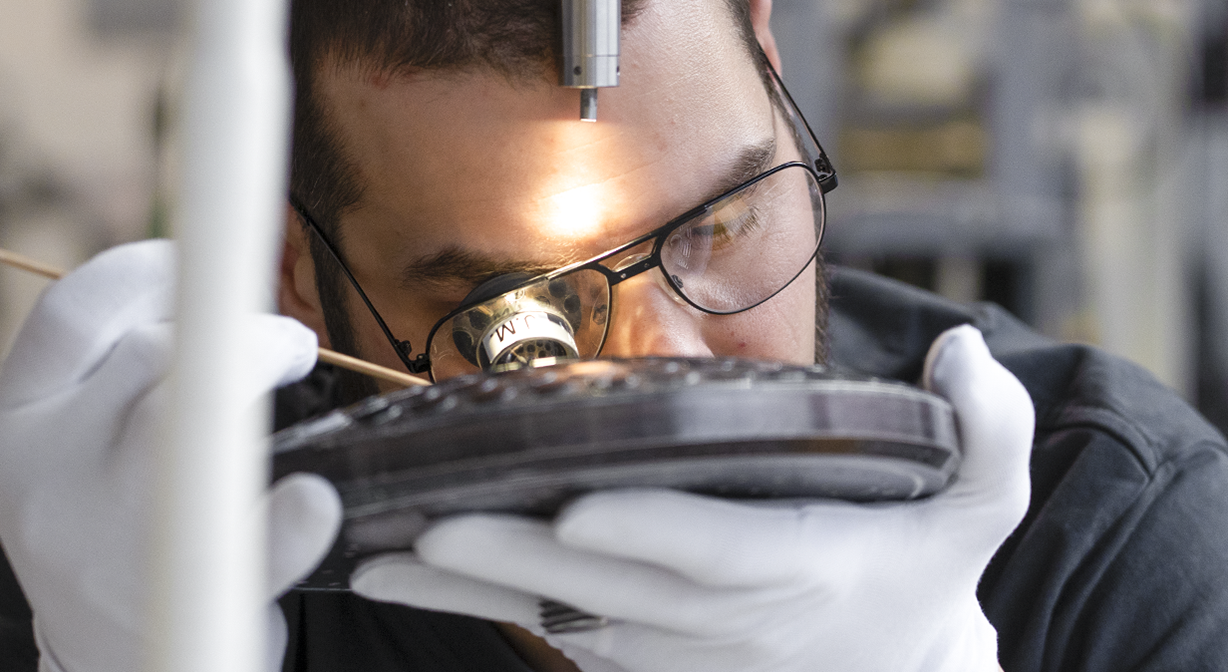
The human hand – the world’s finest tool.
Once we have personally manufactured our products’ key components, it is time to assemble them. And in this respect, we are still a genuine manufacturing firm in many areas. The assembly involves a great deal of very intricate manual work that requires many hours of training and a great deal of experience. We have a few employees who – after years of practice – can pull the fibre-optic bundles consisting of up to 6,000 individual fibres into a blade without breaking a single one. We check each blade afterwards to make sure the process was successful – just to be on the safe side. But you probably would not have expected anything else from us.
One inspection is good. 74 inspections are better.
It is the quality manufacturing process of a product that ensures that defined precision benchmarks are not just replicated once or twice, but thousands of times.
A close look at the manufacturing process of the BETA 200S Direct Ophthalmoscope for example reveals no less than 74 different in-process quality assurance inspections. Some might call this excessive. We simply call it HEINE quality.
Innovation & Durability
We love innovation. Especially when it proves beneficial to our users.
Oliver Heine puts it this way:
“For us it is not necessarily important to be the first with a new development. But we are always the ones that optimally implement new technologies for their application and the diagnosis. We do of course evaluate many new technologies intensively, often very early in their development, but only use them in our instruments when they bring sustainable benefits to the user. Innovation means for us to use new technologies in such a way, that they offer additional value for the doctor and the application. We make no compromises.“

Our instruments last as long as you would expect. Only longer.
Delivering the same performance as on day one – even after many years of daily use. This is not the exception; it’s the rule with our instruments. And the already legendary durability has three very welcome benefits for our users.
Reliability
For one thing, there is reliability. Anyone using a HEINE instrument can rest assured that it will deliver the expected performance. Always, and time and time again.
Affordability
An instrument that lasts for a long time is an affordable instrument. Now, you might say that that is a promise that many make. Right. Only, HEINE goes further – by offering an above-average 5-year guarantee on all instruments. We even offer a 10-year guarantee for our reusable Classic+ F.O. laryngoscope blades. So a HEINE instrument pays for itself – guaranteed.
Sustainability
A particularly durable instrument is a particularly sustainable instrument. Simply because the ecological footprint is greatest during production.
For ecological reasons, we would like to once again point out just how superior our reusable laryngoscope blades are and the issue of ‘reusability versus single-use’. Read more here.
But there is more good news from HEINE: our new company building in Gilching has been built in accordance with the latest requirements set out in the EnEV (Energy Saving Ordinance). In some cases, the building even exceeds the required conditions. Read more about this in the next paragraph.
Ecological responsibility
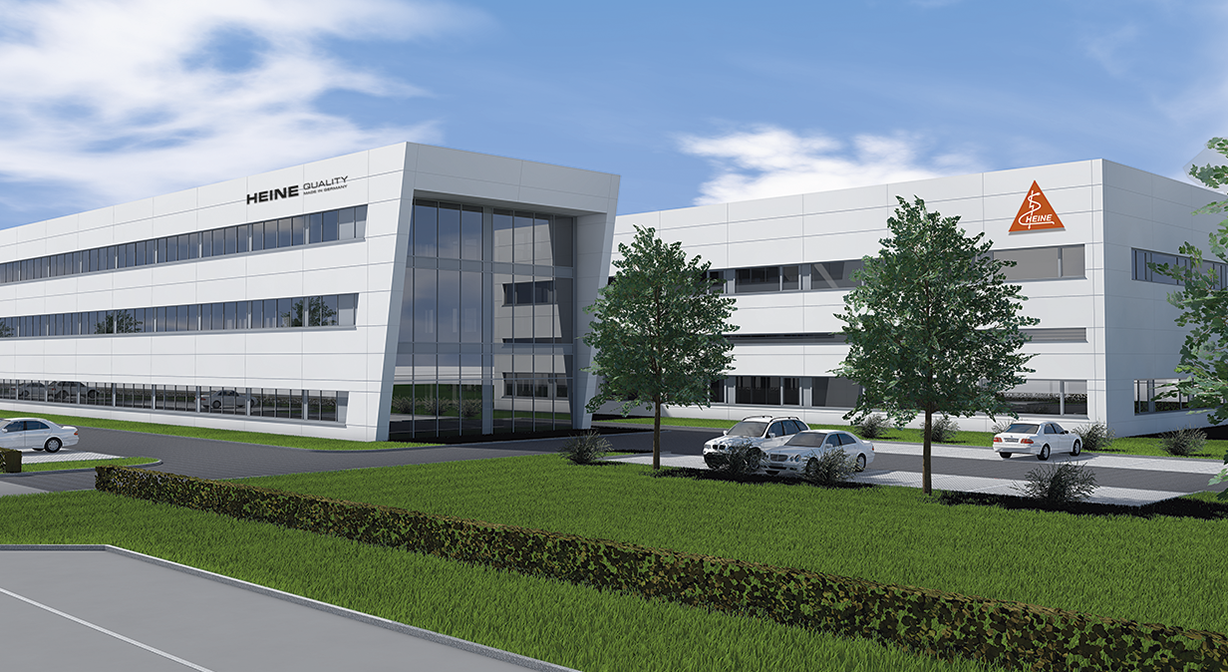
Sustainable right from the start.
HEINE has been one step ahead since moving to its new building in Gilching, south of Munich, in June 2020.
One major goal was to avoid the use of fossil fuels at our new site and cut electricity consumption by 70%. That’s why, for example, the entire building is cooled in summer by a groundwater source heat pump and heated in winter by recovering energy from the waste heat that our machines generate. Greenery covers almost half of the site, as well as the roof.
So the building might look snow-white, but in actual fact it is green.
We live for quality. Sometimes, unfortunately, the weekend gets in our way.
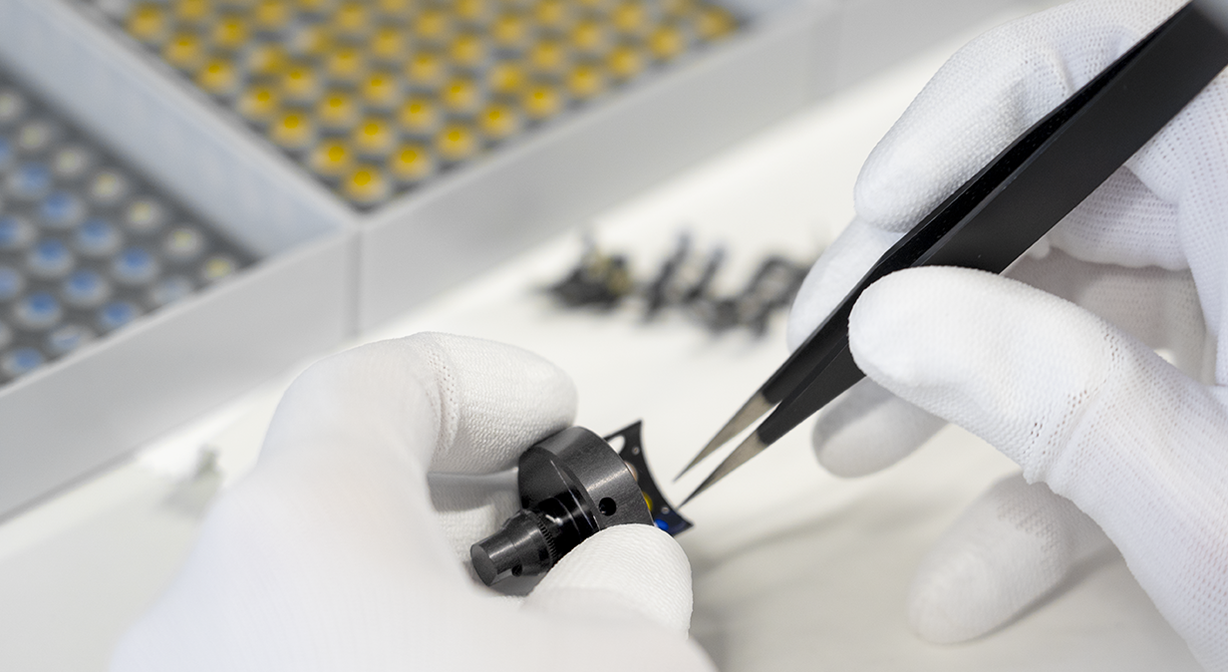
We live and love quality. And – as a consequence – when you love what you do, the result is always top notch. That is why we constantly tinker and improve the quality of our instruments each and every day. All of a sudden, it is Friday evening and we are looking forward to Monday morning. Then we can get back to doing what we love and thinking about quality improvements.
To put it in the words of Oliver Heine, who is the third generation to run the family-owned company:
„Our aim is to develop something that creates additional value in the diagnosis. The doctor should say: The HEINE Instrument has to offer more. All of this defines our development strategy. The strong ambition to always build the best runs in our blood. All HEINE employees live this philosophy: It has to be a Quality Instrument.“
We’ve been doing that for over 75 years now. And that’s exactly what we intend to do in the future.
As an independent family-owned company, we face up to our social, ecological and economic responsibilities. Read more in our CSR Report.